With the ever-increasingly development of modern industry, pressure gauges are indispensable and critical device of most measuring processes. In case of that, a pressure gauge has to be qualified, reliable, accurate and easy to operate to help prevent failure in everyday operations.
Therefore, how a gauge is constructed and configurated is extremely significant for our customers to fully considerate before they make their mind of select one of them. Anyhow, failures can cost time, money and productivity loss.
In today pressure measuring filed, two main categories pressure gauges have been more often than ever involving into our daily life, these are mechanical pressure gauge based on bourdon tube principle and digital pressure gauge also called intelligent gauge. Fortunately, both of them you can find out here at Eastsensor.
Mechanical Bourdon Tube Pressure Gauge
Gauges working with bourdon tubes principles are the most usual pressure measuring devices in our daily life. Mechanical bourdon tube combines a high grade of measuring technology, simple operation, ruggedness and flexibility with the advantages of industrial and cost-effective production. Needing no external power supply, bourdon tube gauges are the best choice for most applications.
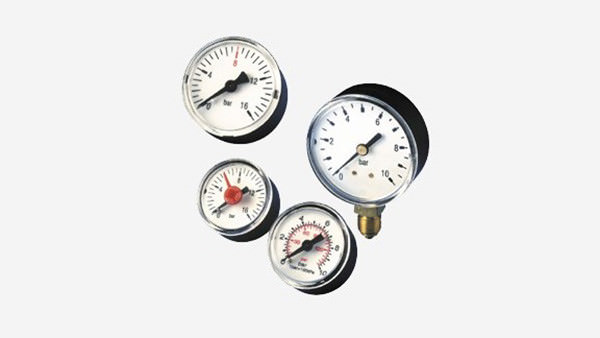
Applications for gauges with a bourdon tube range from highly automated chemical processes, such as, refineries and petrochemical processing, to hydraulic and pneumatic installations. These types of gauges can also be found at all critical process monitoring and safety points in today’s energy industries, from exploration wells and petrochemical plants, to power stations and wastewater operations.
So what exactly it is? Bourdon tube is radially formed tubes with an oval cross-section. The pressure of the measuring medium acts on the inside of the tube and produces a motion in the non-clamped end of the tube. This motion is the measure of the pressure and is indicated via the movement.
The C-shaped Bourdon tubes, formed into an angle of approx. 250°, can be used for pressures up to 60 bar. For higher pressures, Bourdon tubes with several superimposed windings of the same angular diameter (helical tubes) or with a spiral coil in the one plane (spiral tubes) are used.
For detailed information, please refer to ES most sophisticated model of
- ESG501 (General Economical Version),
- ESG502 (Shock Resistance Version)
- ESG503 (Corrosion Resistance Stainless Steel Version).
Although mechanical pressure gauges have their advantages, however like all analog gauges, bourdon tubes cannot make absolute pressure measurements nor are they particularly adept at precision measurements, on the other hand, if accuracy is a key factor when measuring pressure, bourdon tube dial type analog pressure gauges simply cannot compare to how precisely digital pressure gauges measure pressure. Digital pressure gauges offer many other advantages as well.
Digital (Intelligent) Pressure Gauge
A digital pressure gauge is ideal for precise and fast pressure readings. Digital pressure gauges, like the ESG101, ESG102, ESG103 digital pressure gauge, are suitable for a wide range of applications and industries, including mechanical engineering, hydraulics/pneumatics, pumps/compressors, and general service/test operations.
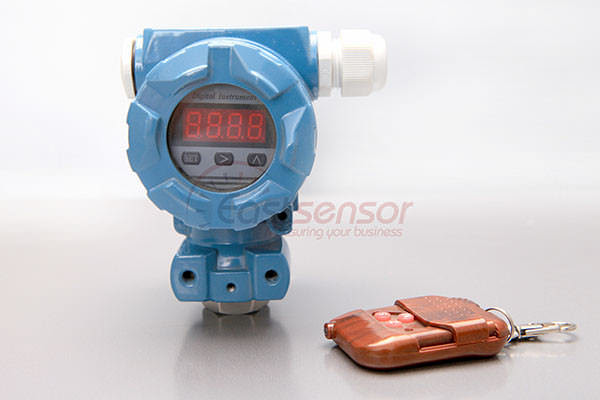
Since they may be transported around in the intervening periods during application, digital pressure gauges feature a stainless steel case, well-designed battery housing, and robust electronics to ensure the longevity of the gauges and subsequent accuracy of readings. Digital pressure gauges can use battery power (ESG103), or loop power (ESG101, ESG102). Both of them have been set forth in details as below.
Battery power
Even the disadvantage to using a battery-powered pressure gauge is that the battery will need to be replaced, and that can be unpredictable however, battery-powered gauges do offer flexibility and convenience while in the field. ESG103 battery based digital pressure gauges that use standard batteries (9V alkaline battery 6LR61) have a long-battery life (2,000 hours or 2 years if serve in power saving model) and consume less power. What is more, the automatic power-off feature will save battery life, and make it last longer.
Loop power
4-20mA loop-powered digital pressure gauges ensure that readings are available at the point of measurement without worrying about battery life. The obvious disadvantage of this method is that wires and a power supply are required. The advantage is that cables that provide power to the unit can also provide an analog output (4~20mA) or digital output (RS485) proportional to the pressure (pls refer to ESG101 digital pressure gauge in our store). If a local display of pressure and an analog output is required, then a pressure transducer that features a local display could be used instead of a loop-powered digital pressure gauge with an analog output and higher accuracy.
Unfortunately and inevitable digital pressure gauges have their disadvantages too as well.
- They are not easy to see full scale or trending
- They are not able to read oscillating values
- They require power (Vdc/Vac)
Which is suitable for you?
A pressure gauge which is a common component in operations from the simplest bike tire gauge to complex gauges for accuracy in industrial and mechanical processing, can measures the pressure level inside a container that holds gas, liquid, vapor, or solid material, helping ensure optimal performance and safety. But not every gauge is created equally or made for every situation.
It is very important that end-users select a pressure gauge that is going to operate the best for them and give them the best results based on what they want to use it for.
At least you should ask yourself 4 questions before you determine whether to employ mechanical or digital pressure gauge for your work.
- What kind of accuracy is needed?
- How much are you willing to spend?
- Do you need any type of outputs?
- Where is this gauge going to be installed?
If an accuracy of 1.0 percent and greater will suffice, and you have a static application and want the least expensive option, a mechanical gauge would work well. While the digital pressure gauge, on the other hand, will provide a precise, accurate reading – no interpretation is needed – and microprocessor technology will allow for several additional programmable functions which will definitely cost more than mechanical type as usual.
Digital gauges sample at various rates (typically 100 or 250 milliseconds) to average out small pulsations and display a constant value. Further, a digital gauge is desirable when the end-user wants both a local and remote pressure indication, and when an automated process control uses pressure as an input to the control system.
For all the modern advantages of the digital gauge, there are some times when the simplicity of the mechanical gauge would work best and be more cost-effective.
For instance, when only a general reading is required (high, medium, low), a mechanical gauge would be the best choice. Mechanical gauges are offered in many different display sizes as well. And one major advantage is that they require no power or batteries.
Some common problem causers are pressure pulsation, which can introduce premature wear in mechanical gauges; vibration process and ambient temperature, which can affect accuracy, repeatability and functionality; and over-pressure spikes.
Other potential problems arise with media that is slurry or has a high concentration of particulate matter that can clog pressure ports; and corrosion, which can damage both mechanical and digital gauges. It’s important to carefully select a gauge with wetted parts that are compatible with the media being sensed. Many of these potential problems can be avoided by using diaphragm seals gauges such as ESG504 and ESG505.
A gauge should be examined and recalibrated at least once a year depending on the intensity of its use. Minor problems can be corrected, and the gauge can be recalibrated and recertified. A gauge that is properly taken care of should last years.
Wrapping up
Pressure gauges generally come with either a male or a female mount that can be situated on the back, top, or base of the dial. The dial varies in range and increment depending on the application to which it is suited. The diameter of the dial varies in size, and the case may be made of steel, aluminum, nylon, or plastic.
The gauge may be filled with liquid such as glycerin oil or silicone oil to dampen the effect of vibration and lubricate the gauge movement. A digital pressure gauge has an LCD screen to display measurements and can measure positive, negative, or differential pressure. It may have features such as selectable measurement units, data hold, minimum and maximum measurements, and data storage.
Just as people have continued to wear dial wristwatches long after the invention of the digital kind, so will people continue to use mechanical pressure gauges. Experts say mechanical devices will remain for those looking for non-powered, free-standing, self-actuated, reasonably priced components.
In terms of future technology, experts say mechanical pressure gauges will improve as modern manufacturing techniques are implemented, such as laser welding, automated assembly, and new materials of construction are added. This will result in more reliable, accurate gauges at a lower cost.
On the digital side, there is believed to be much more opportunity for improvements. New sensor technologies are being developed, which are more cost-effective, consume less power, are accurate, repeatable, and offer a wider range of operating temperatures.
Additional Posts which may be of interest
- Basic Knowledge You Need to Know about Pressure Gauge
- Pressure Switch V.S Pressure Transducer, what’s the difference?
- What is The Difference between Pressure Transducer and Pressure Transmitter?
- Pressure Sensor Technology Comparison
- 10 practices need to considerate before choosing pressure transducer