Like many other process measuring instruments, there are many aspects you need to keep in mind before deciding to buy Pressure Switches however, below are the summary of general rules based on our decade’s experience, for you to follow up.
Basic Types
At low pressures (compressed air and very low pressure hydraulics), diaphragm and bellows movements, sometimes Bourdon tube, are most often used. At high pressures, piston and bourdon tube movements are most common. Snap action contacts seem to be universally used except in Pressure Switches with tilting mercury contacts actuated with a Bourdon tube.
Expected Service Life
Expected life is usually limited by the type of pressure sensing mechanism – Bourdon tube, diaphragm, piston, Belleville spring, etc. The snap action contacts are presumed to have greater life than the sensing mechanism.
If the service life (number of cycles the switch is expected to operate) is less than one million, a Bourdon tube or diaphragm type is indicated. If more than a million cycles, a piston type should be used. An exception to this rule is when the pressure change in a system is small (20% or less, of the adjustable range). Under such conditions a Bourdon tube or diaphragm switch can be used up to 2½ million cycles before metal fatigue or contact failure.
Cycle Life and Cycle Rate
The number of times the switches will be activated will have a direct impact on its longevity. Inherent in their design, electromechanical pressure switches have moving parts that are subject to fatigue affected by factors like magnitude of pressure changes and temperature.
Diaphragm switches will typically provide >500k cycles. A piston design switch can typically provide >1 million cycles and is more reliable than a diaphragm design when subjected to frequent large pressure excursions, pressure surges and spikes. With no moving parts, solid state pressure switches wear is reduced, typically allowing >50 million cycles.
The rate at which a pressure switches is cycled will also impact its longevity. An electromechanical switches with a diaphragm works well for applications with a cycle rate of 25 per minute or less. Piston design mechanical switches are usually suitable for up to 50 cycles per minute. With no moving parts to wear out, a solid state switch should be selected for applications requiring rates that exceed 50 cycles per minute.
Accuracy
Accuracy for a pressure switches is defined differently than accuracy for an instrument. Diaphragm and Bourdon tube pressure switches generally have greater accuracy than piston switches, and would be preferred where accuracy is important, provided they meet requirements for service life and speed of cycling.
The predetermined point at which the pressure switches contact opens or closes is the setpoint. For a pressure switches, accuracy is the ability of the switch to repetitively operate at its setpoint. When in doubt, it is always easier to specify the best accuracy available. But one pays a premium for something that may not be needed. Typically, if the switch is used to alarm, 2% accuracy is sufficient. If one is controlling a process where the error of various devices is additive, then 0.25% accuracy may be absolutely necessary. The accuracy of piston and diaphragm-sealed piston switches is 2%, bourdon tube and diaphragm switches are 0.5%, and solid-state switches 0.25%. Remember, accuracy is referenced at the high end of the operating pressure range and decreases at lower pressure.
FYI, we strongly recommend you ESS202 Intelligent Pressure Switch, for details specification, pls click here to check the data sheet.
For an electromechanical pressure switches with a factory set or user adjusted setpoint relative to a known pressure reference, accuracy is a measure of the switch’s ability to repetitively operate at its adjusted setpoint under the same operating conditions. This is referred to as Repeatability in pressure switches specifications.
Because a solid state switch setpoint can be adjusted with calibrated dials, knobs, or a keypad and display, specifications will include both a setting accuracy value and a repeatability value. Pressure switches are typically available with accuracies from 0.25% to 2% and cost increases with accuracy. To avoid paying a premium for unnecessary accuracy, consider the needs of the application. An accuracy of 2% is probably sufficient for a simple alarming application, but controlling a critical process may call for a higher accuracy switch.
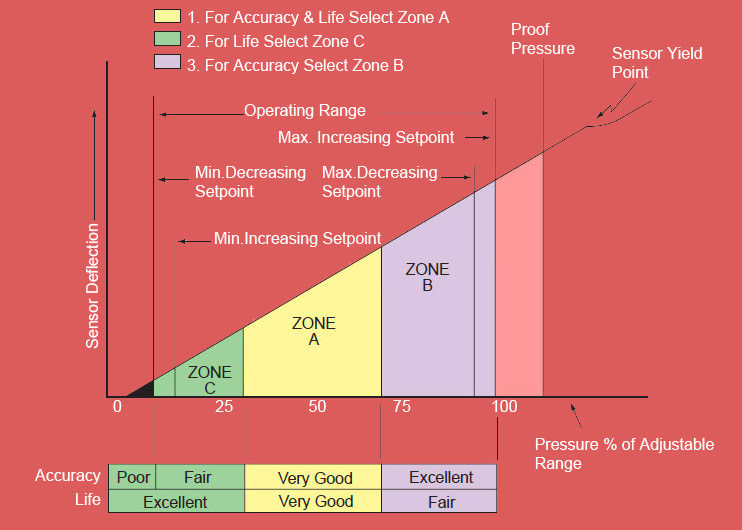
Above figure show: On switches with diaphragm and Bourdon tube movements, greatest accuracy is in the upper 65%, best life factor in the lower 65%, and the best combination is usually in the middle 30% of its working range (Zone A).
Adjustable Range
The term “working range” defines the pressure range a switch may see under normal working conditions. This is normally the adjustable range.
For greatest accuracy the set point should fall in the upper 65% of the adjustable range. But for the most favorable life factor the set point should be in the lower 65% of the adjustable range.
Therefore, the most favorable combination of accuracy and life factor lies in the middle 30% of the adjustable range and this is illustrated in above diagram. This general rule applies to diaphragm and Bourdon tube pressure switches. Piston switches have a more nearly uniform accuracy and life factor over their adjustable range.
Both electromechanical and solid state switches are commonly available to sense vacuum, positive pressures up to thousands of psi, and compound ranges of vacuum to positive pressure.
Electromechanical switches are typically available with a factory setting, or with a blind adjustment capability set by the user relative to an external pressure reference such as a pressure gauge or known pressure value.
Electromechanical switch setpoints can be set to activate upon an increased or decreased pressure. Solid state switch setpoints are set either by calibrated dials, knobs, or entered digitally with a keypad and display.
Deadband
Deadband is the difference in pressure between the switch setpoint and reset point. For example, if a switch is set to activate at 100 psi on an increasing pressure, the switch will close when the pressure rises to 100 psi. When the pressure drops to the reset point of 90 psi, the switch will open. The deadband is 10 psi, the difference between the setpoint (100 psi) and the reset point (90 psi).
For electromechanical switches, deadband can be adjustable but is typically a fixed value, or automatically increases linearly as the setpoint is increased through the adjustable setpoint range.
For solid state switches, the deadband is typically fully adjustable up to 100% of the full operating pressure range. As a general rule a narrow deadband is used in alarm circuits while a wider deadband is better suited for control circuit applications.
Proof and Burst Pressures
Overpressure ratings include proof and burst pressure specifications. Proof pressure is the amount of overpressure that can be applied to the switches without causing damage. The pressure switches can be exposed to pressure reaching the proof pressure rating, and be expected to work properly when the pressure returns to within the rated operating pressure range.
Burst pressure is the amount of overpressure applied at which switches will certainly be damaged. Physical damage to the pressure switches may occur at any point between the proof pressure and burst pressure.
Because proof pressure ratings are determined in a laboratory under controlled conditions including rate of pressure change and temperature, they should be considered a reference value. It is not uncommon for switches in the field to experience pressure surges and spikes that cause damage if a switch with too low of a proof pressure rating was selected. Typically solid state switches have lower proof pressure ratings and are most sensitive to overpressure conditions.
Electromechanical switches with a diaphragm generally have higher overpressure ratings than solid state switches. Piston design switches have very high overpressure ratings and are the most reliable when subjected to pressure surges or spikes, and applications where the normal working pressure is above the nominal range of the switch.
If pressure surges or spikes are anticipated in an application, a pressure switches with a high proof pressure should be selected to avoid damage.
System pressure
Knowing your normal and maximum system pressures will help in selecting a switch with appropriate minimum and maximum operating parameters. Once your set point is established, other factors to consider are vacuum and/or surge pressure that could affect switch operation.
This would involve maximum working pressure, over range pressure, and proof pressure specifications of a pressure switches. The relationship between set point and system pressure has a direct effect on switch performance and life.
Electrical considerations
Micro-switches are available in a variety of configurations. The most common for electro-mechanical switches is 15A, 480VAC SPDT (single pole, double throw). The advantage of a SPDT micro-switch is that it offers wiring flexibility to either open or close on pressure change. Other micro-switches available include 1A with gold contacts, useful when working with a PLC, or at the upper end, 30A when switching certain high voltage heaters or motors.
Adjustable micro-switches help with deadband adjustment. A DPDT (double pole, double throw) micro-switch would provide two simultaneous functions off of one micro-switch. If a low-high limit alarm and shutdown were required, there are pressure switches that include two SPDT micro-switches that are independently settable.
An electronic switch would use solid-state relays to change states. Like an electro-mechanical switch, the electronic switch can be programmed to open or close on rising or falling pressure. There are different capacities for switching voltage and current depending upon the application requirements.
Electrical Characteristics
Electromechanical pressure switches harness the pressure of the medium being sensed to mechanically operate a snap-acting switch – no external power supply is required for the pressure switches to operate. Typically, electromechanical pressure switches are provided with SPDT or DPDT contacts rated for 3 to 15 amps and voltages from 120VAC to 480VAC. With solid state switches, an external power supply, usually 24VDC, is necessary to power the electronic circuitry inside the switch. The outputs of solid state switches are typically normally-open and normally-closed transistor switching outputs rated for about 500mA and 30VDC.
Process media and wetted parts
The pressure connection and sensor are known as wetted parts since they come into direct contact with the process media. Sensor material is either elastomer (i.e. Buna-N, Teflon®) or metallic (i.e. Brass, Stainless Steel) with metallic or composite pressure connections.
The process media must be compatible with the wetted parts material. Process media temperature should also be considered as each of the different wetted materials would have differing operating properties.
For both electromechanical and solid state switches, determining the chemical compatibility of switches with the medium sensed is a critical element in the longevity of the pressure switches.
Wetted parts are the parts of the switches that actually come in direct contact with the medium being sensed, and their material composition is identified in switches specifications. The wetted parts will include the pressure sensing port of the switch, the diaphragm, bellows, bourdon tube, or piston and any O-ring seals.
Chemical resistance charts and databases are readily available on the Internet and may be used to determine the compatibility of switches wetted parts with the chemicals encountered in the measured medium.
A switch with a brass pressure sensing port and elastomeric diaphragm (such as Buna N or Viton) may work well for some applications but will not last as long as a pressure switches with the chemical resistance of a weld-sealed stainless steel diaphragm and sensing port in many industrial applications.
Pressure switches mounting
If the unit is to be installed directly onto the process, there are many methods of installation.
Typically a 1/8”, 1/4”, or 1/2” NPT (national pipe thread taper) connection is used with a mating fitting to secure the pressure switches to the process. There are also straight threaded (SAE, BSPT) connections, flush mount connections, and sanitary connections.
Check details about Thread Types for process connection.
The switches may be mounted directly in the process line using the threaded connection, a manifold, or flange; or the enclosure could be bolted to a mounting plate or other plane to secure it. If heavy vibration is present, you may choose to use a remote diaphragm seal with the pressure switches. The diaphragm seal mates with the process connection while the switches enclosure is mounted securely away from the vibration.
Process environment
It is important to know what type of environment the switches would be installed in – hazardous or ordinary location; indoors or outdoors; exposed to salt air; inside a control panel; in high ambient temperature. These are just some of the factors to consider so the right enclosure type is chosen. Enclosure types come in many shapes, sizes, and materials. They also conform to various industry and third-party approval standards.
Electronic switches can be used to replace electro-mechanical switches when SIL is needed for safety applications. There are also electro-mechanical switches without enclosures; typically used in OEM, non-hazardous locations where the environment is benign.
Types of Switch Action
Standard switches sense a single pressure source and open or close a single set of contacts. Differential switches have two connections and sense the pressure difference across a circuit.
Dual switches sense a high and low limit on the same pressure source, and actuate two sets of electrical contacts. Wide range dual pressure sensing can be accomplished with two standard switches. See diagram below.
Additional Posts which may be of interest
- Which Pressure Switch is suitable for you?
- Things you need to know about Diaphragm Pressure Gauges
- Do you really know your pressure sensor accuracy?
- Basic Knowledge You Need to Know about Pressure Gauge
- How to select Pressure Gauge?
- Pressure Switch V.S Pressure Transducer, what’s the difference?
- What is The Difference between Pressure Transducer and Pressure Transmitter?
- Pressure Sensor Technology Comparison
- 10 practices need to considerate before choosing pressure transducer
- What’s the role of smart sensors in Industry 4.0?
- How sensor has been rocking our world?