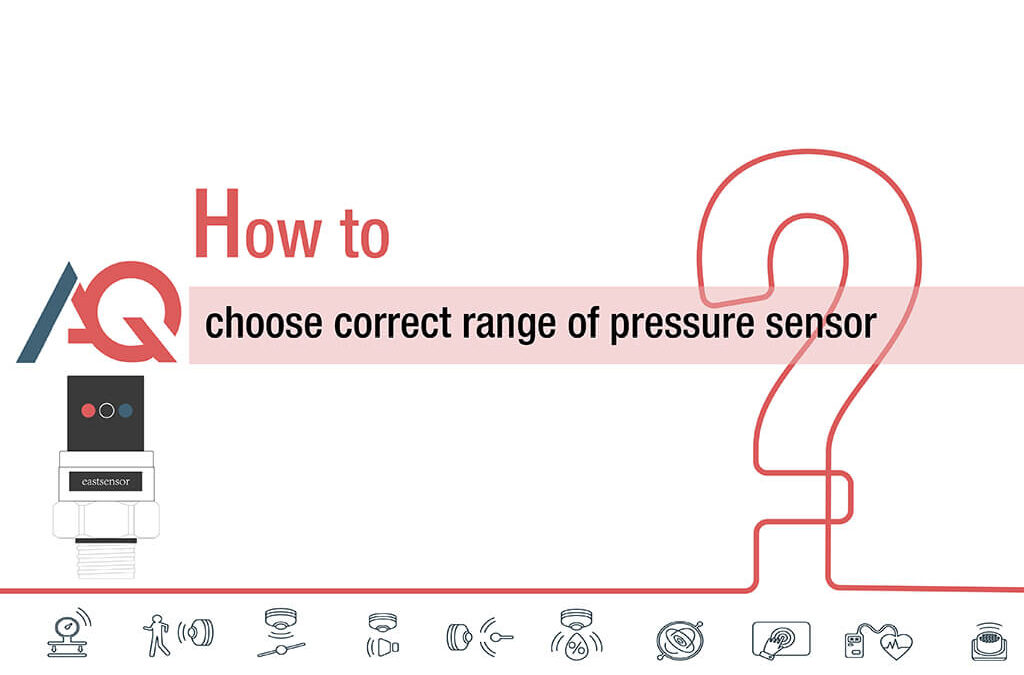
Pressure Range: How to choose it for pressure sensor
Pressure range categorify
The required pressure range should be measured accurately by pressure sensor, withstand the environmental conditions, and meet the performance specifications of the particular application. So, understanding the specific pressure ranges for different industries and applications is essential when selecting the appropriate pressure sensor.
Categorizing pressure range according to industry needs is an important aspect of pressure sensor selection. Different industries have varying requirements based on their specific processes and applications, however the normal practice to categorify pressure range goes as below, you can make reference.
- Vacuum: < 0 bar (absolute)
- Low Pressure: 0 to 10 bar
- Medium Pressure: 10 to 100 bar
- High Pressure: 100 to 1,000 bar
- Ultra-High Pressure: > 1,000 bar
A) Vacuum: < 0 bar (absolute)
- The vacuum pressure range refers to pressures below atmospheric pressure, which is 0 bar (absolute).
- This range is typically used in applications where the pressure needs to be significantly lower than the surrounding atmospheric pressure, such as in vacuum chambers, vacuum pumps, and some industrial processes.
- Pressure sensors used in vacuum applications must be capable of accurately measuring very low pressures, often down to a few millibars or even microbars.
B) Low Pressure: 0 to 10 bar
- The low-pressure range covers pressures from atmospheric pressure (0 bar) up to 10 bar.
- This range is commonly used in applications such as pneumatic systems, HVAC (Heating, Ventilation, and Air Conditioning) systems, and some industrial processes.
- Pressure sensors in this range need to have high sensitivity and accuracy to effectively measure the relatively small pressure changes.
C) Medium Pressure: 10 to 100 bar
- The medium-pressure range covers pressures from 10 bar to 100 bar.
- This range is often encountered in hydraulic systems, compressors, and high-pressure industrial processes.
- Pressure sensors in this range must be robust and able to withstand the higher pressures while maintaining accuracy and reliability.
D) High Pressure: 100 to 1,000 bar
- The high-pressure range covers pressures from 100 bar to 1,000 bar.
- This range is commonly found in applications such as high-pressure hydraulic systems, fuel injection systems, and some chemical processing equipment.
- Pressure sensors in this range must be designed with materials and construction techniques that can withstand the extreme pressures, while also providing accurate and stable measurements.
E) Ultra-High Pressure: > 1,000 bar
- The ultra-high-pressure range refers to pressures greater than 1,000 bar.
- This range is encountered in specialized applications, such as high-pressure processing, ammunition manufacturing, and some research and development facilities.
- Pressure sensors used in this range must be engineered with advanced materials and specialized design techniques to handle the incredibly high pressures, while maintaining a high level of performance and reliability.
No. | Application | Pressure Range | Strength |
---|---|---|---|
1 | Vacuum chambers | 10^-10 to 10^-3 bar | Very Low |
2 | Vacuum processes | -1 to 0 bar | Very Low |
3 | Respiratory equipment | -0.1 to 0.1 bar | Very Low |
4 | Ventilation systems | 0 to 0.1 bar | Very Low |
5 | Blood pressure monitoring | 0 to 0.5 bar | Very Low |
6 | Cabin pressure | 0 to 1 bar | Very Low |
7 | Sterilization processes | 0 to 5 bar | Low |
8 | Tire pressure | 0 to 5 bar | Low |
9 | Pasteurization | 0 to 5 bar | Low |
10 | Fuel systems | 0 to 6 bar | Low |
11 | Engine oil pressure | 0 to 10 bar | Low |
12 | Pneumatic systems | 0 to 10 bar | Low |
13 | Carbonation processes | 0 to 10 bar | Low |
14 | Pump monitoring | 0 to 10 bar | Low |
15 | Chemical vapor deposition | 0 to 10 bar | Low |
16 | Filtration systems | 0 to 20 bar | Medium |
17 | Water distribution systems | 0 to 20 bar | Medium |
18 | Air conditioning systems | 0 to 30 bar | Medium |
19 | Refrigerant pressure | 0 to 50 bar | Medium |
20 | Reverse osmosis | 0 to 80 bar | Medium |
21 | Hydroelectric systems | 0 to 100 bar | Medium |
22 | Pipeline monitoring | 0 to 100 bar | Medium |
23 | Nuclear reactors | 0 to 150 bar | High |
24 | Gas delivery systems | 0 to 200 bar | High |
25 | Steam turbines | 0 to 300 bar | High |
26 | Hydraulic systems | 0 to 350 bar | High |
27 | Hydraulic systems | 0 to 700 bar | High |
28 | Wellhead pressure | 0 to 1,000 bar | High |
29 | Subsea applications | 0 to 1,500 bar | Very High |
30 | Fuel injection systems | 0 to 2,000 bar | Very High |
Pressure range for different sensing ways
The pressure ranges for each technology are primarily determined by the inherent material properties, manufacturing processes, and sensing mechanisms used in the pressure sensors.
To figure out the pressure range for different sensing technology is not a easy job however, let me make an assumption: let’s say all other conditions are the same, and we’re only considering the minimum and maximum ranges of different sensing technologies.
0-0.07bar-1000bar |Silicon Piezo-resistance (Diffused)
Silicon piezo-resistive sensors are based on the piezoresistive effect, where the resistance of the silicon material changes when subjected to pressure. Diffused silicon piezo-resistive sensors have a lower pressure sensitivity compared to monocrystalline silicon, limiting their minimum pressure range to around 100 mbar (10Kpa), or even 70mbar (7Kpa). However, they can withstand higher pressures, up to 1000 bar (100Mpa), due to the robustness of the silicon material and the manufacturing process.
- Minimum pressure range: 0 to 100 mbar (0 to 10 Kpa)
- Maximum pressure range: 0 to 1000 bar (0-100 Mpa)
0-0.002bar-250bar | Silicon Piezo-resistance (Monocrystalline)
Monocrystalline silicon piezo-resistive sensors have a higher-pressure sensitivity compared to the diffused version, allowing them to measure lower pressures, down to around 2 mbar.
The monocrystalline structure of the silicon material provides better mechanical properties, enabling these sensors to withstand significantly higher pressures, up to 250 bar.
- Minimum pressure range: 0 to 2 mbar (0 to 0.2 Kpa)
- Maximum pressure range: 0 to 250 bar (0-25 Mpa)
0-0.5bar-480bar-600bar |Ceramic Piezo-resistance (Thick-film)
Ceramic piezo-resistive sensors, specifically the thick-film type, leverage the piezoresistive effect in ceramic materials, such as alumina or zirconia, are also known for their high temperature stability and durability, making them suitable for harsh environments.
What is more, ceramic materials have excellent both the anti-corrosion ability and mechanical properties, allowing them to work under some extreme environments to withstand high pressures, up to 480 bar (Monolithic) and 600 bar (Flush diaphragm) , while maintaining a minimum pressure range of around 500 mbar.
- Minimum pressure range: 0 to 500 mbar (0 to 50 Kpa)
- Maximum pressure range: 0 to 600 bar
0-0.1bar-100bar |Ceramic Capacitive
Ceramic capacitive pressure sensors work on the principle of a changing capacitance when subjected to pressure.
Ceramic materials, such as alumina or lead zirconate titanate (PZT), provide high pressure sensitivity and can measure pressures as low as 100 mbar.
However, the maximum pressure range for ceramic capacitive sensors is typically lower than piezo-resistive technologies, around 100 bar, due to the inherent limitations of the capacitive sensing mechanism.
- Minimum pressure range: 0 to 100 mbar (0 to 10 Kpa)
- Maximum pressure range: 0 to 100 bar (0-10Mpa)
0-0.001bar-250bar |Metal Capacitive
Metal capacitive pressure sensors use a metal diaphragm that deflects when subjected to pressure, changing the capacitance between the diaphragm and a fixed electrode.
Metal materials, such as stainless steel or Inconel, provide excellent mechanical properties, allowing metal capacitive sensors to measure pressures up to 250 bar.
The minimum pressure range of 100pa (0.1 Kpa) is achievable due to the sensitive capacitive sensing mechanism.
- Minimum pressure range: 0 to 100pa (0.1 Kpa)
- Maximum pressure range: 0 to 250 bar (25 Mpa)
0-4bar-2200bar|Thin Film Sputtering
Thin film sputtering is a manufacturing process that deposits thin layers of materials, such as metal or ceramic, onto a substrate to create pressure-sensing elements.
The thin film sensing elements can measure pressures as low as 4 bar, while the underlying substrate and manufacturing techniques allow for a maximum pressure range of up to 2,200 bar.
Thin film sputtering enables the creation of compact and highly sensitive pressure sensors.
- Minimum pressure range: 0 to 4 bar
- Maximum pressure range: 0 to 2,200 bar
0-7bar-700bar|Glass micro-Dissolution
Glass micro-dissolution pressure sensors utilize the principle of a glass diaphragm that deforms when subjected to pressure, changing the electrical characteristics of the sensor.
The glass material provides excellent mechanical properties, allowing these sensors to measure pressures up to 700 bar.
The minimum pressure range of 7 bar is achievable due to the sensitivity of the glass diaphragm and the supporting electronics.
- Minimum pressure range: 0 to 7 bar
- Maximum pressure range: 0 to 700 bar
4 tips to select correct pressure range for sensor
How to choose correct range for industry application? That is a common question for many industries, here I have wrap up several basic and common rules that people refer to in daily use. I’ll explain these rules with examples and data to illustrate each point clearly.
1. Rule of Safety Factor:
The safety factor is the most important rule, please pay attention that you need always to choose a pressure sensor with a range higher than the maximum expected pressure, typically by a factor of 1.3 to 2.
For example, in a hydraulic system where the maximum operating pressure is 200 bar, so you might choose a sensor with a range of 260-400 bar.
Calculation: 200 bar * 1.3 = 260 bar (minimum), 200 bar * 2 = 400 bar (maximum)
2. Rule of Resolution:
Select a sensor range that allows for adequate resolution of your measurements. Aim for using at least 25%, at most 80% of the full scale.
For example, if you need to measure pressures between 0 and 5 bar with good resolution, don’t choose a 0-100 bar sensor. Instead, opt for a 0-20 bar sensor, 0-8 bar will be also one of the workable solutions.
Calculation: 5 bar / 20 bar = 25% of full scale; 5 bar / 8 bar = 62% of full scale.
3. Rule of Overload Protection
It is also need to consider the maximum pressure the sensor can withstand without damage, which is typically 1.5 to 2 times the full scale.
For example: A 0-100 bar sensor might have an overload protection of 150-200 bar.
Calculation: 100 bar * 1.5 = 150 bar, 100 bar * 2 = 200 bar
4. Rule of Accuracy Requirements:
Select a sensor with an accuracy that meets or exceeds your application needs. Accuracy is often expressed as a percentage of full scale.
For example: If you need to measure a pressure of 10 bar ±0.1 bar, you need a sensor with at least 1% accuracy on a 0-20 bar scale.
Calculation: 0.1 bar / 10 bar = 1% accuracy needed
The Sensitivity Seesaw: Balancing Pressure Range and Sensor Sensitivity
First things first – what is sensitivity anyway? In simple terms, it’s how much your sensor’s output changes when the pressure changes. For example, if your sensor’s sensitivity is 5 mV/bar, you’ll see a 5 mV change in output for every 1 bar change in pressure. Easy peasy, right?
The Inverse Relationship: More Range, Less Sensitivity
There’s this sneaky inverse relationship between pressure range and sensitivity. It’s like a seesaw – when one goes up, the other goes down. So, if you crank up the pressure range, your sensitivity takes a nosedive.
Let’s break it down with some real numbers:
Imagine you’ve got two sensors, both with a full-scale output of 100 mV (pretty standard stuff).
- Sensor A: 0-10 bar range. Sensitivity = 100 mV / 10 bar = 10 mV/bar
- Sensor B: 0-100 bar range. Sensitivity = 100 mV / 100 bar = 1 mV/bar
See what happened there?
Sensor B can handle way more pressure, but it’s also way less sensitive. It’s like trying to hear a pin drop in a noisy factory versus a quiet library.
Now, here’s where things get tricky. That lower sensitivity can lead to some real headaches, especially when you’re dealing with pressures at the low end of your range. Your resolution takes a hit, and your signal-to-noise ratio goes out the window.
Picture this: You’ve got a 0-1000 bar sensor, but you’re trying to measure pressures below 10 bar. Good luck with that! It’s like trying to weigh a feather on a scale designed for elephants.
So, what do we do about this sensitivity problem? Well, one common trick is to use signal amplification. It’s like turning up the volume on a quiet speaker. But here’s the catch – when you amplify the signal, you’re also cranking up the noise. It’s not a perfect solution, but sometimes it’s the best we’ve got.
Let’s say you’re working on a hydraulic system that operates between 50-200 bar. You might be tempted to go for a 0-1000 bar sensor for the overload protection. But hold your horses! A 0-250 bar sensor might give you better sensitivity in your actual operating range.
The Takeaway
Remember, – in the world of pressure sensors, it’s all about finding the right balance. Don’t get dazzled by big numbers if you don’t need them. Think about your actual application, and choose a sensor that gives you the best sensitivity in the range you’re actually using.
Two typical cases
Big range sensor measures small pressure
Let’s chat about a common mistake I’ve seen way too often in the field: using a high-range pressure sensor to measure low pressures. It’s like bringing a bazooka to a water gun fight – overkill and potentially problematic. Let me break it down for you.
The Sensitivity Struggle
First off, let’s talk sensitivity. Using a big pressure sensor for small pressures is like trying to hear a whisper at a rock concert. A 1000 bar sensor might only twitch 0.1 mV for a 1 bar change, while a 10 bar sensor would give you a robust 10 mV signal. See the problem?
Resolution Revolution
Now, imagine you’re trying to measure the depth of a puddle with a yardstick marked in feet. That’s what happens to your resolution. With a 12-bit ADC, a 1000 bar sensor gives you chunky 0.24 bar steps. A 10 bar sensor? A much nicer 0.0024 bar. Details matter, folks!
Accuracy Apocalypse
Here’s where it gets really messy. Let’s say you’ve got a 1000 bar sensor with 0.1% accuracy. Sounds great, right? Well, when you’re measuring 5 bar, that 0.1% translates to a whopping 20% error. Yikes! A properly sized 10 bar sensor would nail it with just 0.2% error.
Noise Nightmare.
Ever tried to have a quiet conversation next to a jet engine? That’s what it’s like for the poor signal from your oversized sensor. A teensy 0.1 mV change from a 1000 bar sensor could easily get lost in the noise, while a 10 mV change from a right-sized sensor stands out loud and clear.
Small range sensor measures big pressure
Another common misconception is that a sensor can be used to measure pressures significantly beyond its rated range.
When a sensor is exposed to pressures exceeding its maximum rated capacity, it typically saturates at its full-scale output and cause temporary or even permanent damage to pressure sensor after overload.
Click to check the details how overload affect pressure sensor performance,
While it may be still tempting to use available small range sensors for high-pressure applications, the risks far outweigh any perceived benefits. So proper sensor selection is crucial for system reliability, accuracy, and safety.
Always consult with sensor manufacturers or experienced instrumentation engineers when in doubt about the appropriate sensor range for your application.