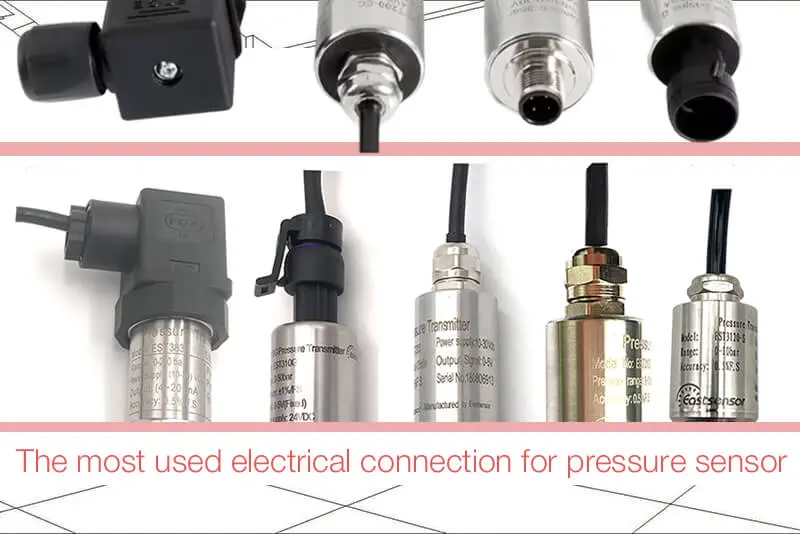
Pressure Sensor Electrical Connection
Regardless of the sensor technology employed, the purpose remains the same: converting a pressure signal into an electrical signal, which can then be amplified, conditioned, and read by a control system or display; in this regard, the role of electrical connections in a pressure sensor cannot be overstated.
These connections transmit the electrical signal from the pressure sensor to its corresponding system. Ensuring that these connections are reliable and of high quality is essential to prevent issues such as inaccurate readings, fluctuations in the output signal, or even complete failure of the device.
The Most Popular Electrical Connection Types
As an engineer experienced in pressure sensors, I have encountered several common types of electrical connections widely used in these devices. The four main types of electrical connections for pressure sensors are wire leads, terminal blocks, connectors, and PCB mounting. They each have their advantages and specific use cases, according to the requirements of the application.
1.Wire Leads:
Type 1: Wire Leads, or you can call it flying leads
Feature: Simplicity and Versatility
Details: Wire leads are simple wires connected directly to the pressure sensor. They offer flexibility and versatility when it comes to connecting the sensor to the designated system. Wire leads are often used in situations that require custom cable lengths or when the pressure sensor needs to be relocated frequently.
2.Terminal Blocks:
Type 2: Terminal Blocks:
Feature: Secure and User-friendly
Details: Terminal blocks provide a more secure and user-friendly connection compared to wire leads. With terminal blocks, the pressure sensor has a designated terminal strip where the connections are made using screws or push-fit mechanisms. This ensures secure connections, easy accessibility, and a lower likelihood of becoming loose or disconnected during use.
3.Connectors:
Type 3: Connectors:
Feature: Environmental Resistance and Ease of Use
Details: Connectors are an excellent choice for applications where environmental resistance, such as protection against moisture, dust, or chemicals, is essential. They offer different levels of ingress protection (IP) and accommodate various types of mating connectors for easy integration with the end application. Connectors are also designed for quick and easy connection and disconnection, simplifying routine maintenance and replacement processes.
4.PCB Mounting:
Type 4: PCB Mounting:
Features: A Compact, Integrated Solution
Details: PCB mounting is a method where the pressure sensor is directly soldered onto a printed circuit board, integrating it with the entire system. This type of mounting offers a compact and stable solution, reducing the need for connectors or wires. It is an excellent choice for applications with limited space or where extreme vibration resistance is required.
The most common electrical connectors
Below I will provide valuable information on four kinds of common-use electrical connectors for pressure sensor design and production; they are
- DIN43650 (A/B),
- Packard connector,
- M12,
- Waterproof Plug Cable.
I will emphasize each type’s technical aspects and benefits and show the features, details, pros, and cons of each type, all for your further reference.
1.Types 1 DIN43650
- Features: Precision and Industry Standardization
- Details: In my experience, DIN43650 connectors have been a top choice for pressure sensor electrical connections, offering precision and industry standardization. The German national standard DIN 43650 (Deutsches Institut für Normung) defines these connectors’ dimensions and technical features, facilitating interoperability and compatibility among various devices in industrial applications.
Moreover, DIN43650 connectors is a screw terminal design, ensuring secure and stable connections. They typically come in two widely-accepted form factors: type A, type B, and C.
- The type A connector provides an 18 mm distance between connection pins; type A always be used in hydraulics and pneumatics
- The type B connector has a 10 mm-11mm distance, type B can also be used in hydraulics and pneumatics applications, what’s more, type B save space a lot than A.
- The type C, the smallest one, it has two versions, the 8 mm (two pins plus earth) and the 9.4 mm (three pins plus earth).
No matter A, B, or C, these connectors often feature IP65 or IP67 ingress protection, safeguarding against dust and water ingress for reliable performance in harsh environments.
Let’s talk about the pros and cons of DIN43650 when it comes to pressure transmitters.
- Pros:
- Industry-standard dimensions and technical features: Ensures compatibility and interoperability with various devices in industrial applications.
- Screw terminal design: Provides secure and stable connections.
- IP65 or IP67 ingress protection: Protects against dust and water ingress for reliable performance in harsh environments.
- Cons:
- Larger form factor: This may not be ideal for applications with limited space.
- No quick-disconnect option: Requires a screwdriver for secure installation and removal.
2.Type 2: Packard:
- Feature: Adoption and Automotive Excellence.
- Details: These connectors, often used by General Motors (GM) and other automotive manufacturers, boast a compact design that excels in applications with limited space. Packard connectors employ a push-in terminal design, simplifying installation and removal while maintaining a secure electrical connection.
What I find most advantageous about Packard connectors is their environmental sealing, which often features silicone rubber seals preventing ingress of contaminants such as dirt, moisture, and automotive fluids. This protection ensures reliable connections in demanding automotive pressure sensor applications.
Let’s talk about the pros and cons of Packard when it comes to pressure transmitters.
- Pros:
- Compact design: Suitable for applications with limited space.
- Push-in terminal design: Simplifies installation and removal while maintaining a secure connection.
- Environmental sealing: Silicone rubber seals protect against contaminants such as dirt, moisture, and automotive fluids.
- Cons:
- Specific to automotive applications: Limited versatility compared to other connector types.
3. M12 Connector:
- Features: Versatility and Rapid Installation
- Details: The M12 connectors are circular connectors with 12 mm mating threads, designed for quick connection and disconnection in various industrial applications, including automation, process control, and instrumentation.
One of the most persuasive aspects of M12 connectors is their wide range of available pin configurations, accommodating different voltage and current requirements. Common configurations include 3, 4, 5, and 8-pin layouts. These connectors also boast a high level of ingress protection, typically IP67 or IP68, ensuring excellent performance in environments with exposure to dust, moisture, or chemicals.
Let’s talk about the pros and cons of M12 Connector when it comes to pressure transmitters.
- Pros:
- Versatile: Suitable for various industrial applications, including automation, process control, and instrumentation.
- Quick connection and disconnection: Simplify installation and maintenance.
- Wide range of pin configurations: Accommodates different voltage and current requirements.
- High ingress protection: IP67 or IP68 rating protects against dust, moisture, or chemicals.
- Cons: Less compact for applications with minimal space.
4. Waterproof Cable:
- Features: Advanced Protection and Durability
- Details: Waterproof Plug Cables feature specially-engineered jackets and seals, providing excellent resistance to water and moisture ingress, making them particularly well-suited for outdoor and underwater applications.
When selecting a waterproof cable for your pressure sensor, it is crucial to consider the IP rating to ensure adequate protection for your specific application. Commonly used ratings in waterproof cables include IP65, IP67, and IP68, each offering varying levels of protection against dust and moisture.
Let’s talk about the pros and cons of Waterproof Cable connectors when it comes to pressure transmitters.
- Pros:
- Advanced protection: Specially-engineered jackets and seals offer excellent water and moisture ingress resistance.
- Suitable for outdoor and underwater applications: Provides reliable connections in harsh environments.
- Covers a range of protection options: IP65, IP67, IP68 ingress protection ratings:
- Cons:
- Connector type dependent: Cable’s overall performance may vary based on the attached connector.
3 Regular wires connection types
In this section, let’s explore the relevance and benefits of various pressure sensor electrical connections, specifically focusing on 2-wire, 3-wire, and 4-wire connection systems. Each connection type has specific advantages and applications, so understanding these systems in detail will prove invaluable when making pressure sensor electrical connection decisions.
To save time, you can find the highlight feature below for each if you are busy.
- 2-wire Simplicity and Cost-Efficiency
- 3-wire Increased Versatility and Stability
- 4-wire Ultimate Precision and Performance
For more details, let’s go as following.
1. 2-Wire Connection:
A 2-wire connection is the simplest and often most cost-effective method for connecting pressure sensors. In this system, the same two wires act as both power supply and output signal transmission, streamlining the design and installation process. This configuration is suitable for devices operating in a current loop, typically using a 4-20 mA output signal, which is a widely accepted standard in industrial applications.
Advantages of the 2-wire connection include its low cost, simple design, and ease of installation. However, it can be susceptible to voltage drops due to long cable runs, making accurate voltage measurements challenging in such scenarios.
2, 3-Wire Connection:
A 3-wire connection is a widely popular choice for pressure sensor electrical connections, offering increased versatility and stability compared to the 2-wire system. In configuration, the three wires are connected to the power supply, ground, and output signal, allowing for a separate return path for the signal and improving measurement accuracy. This connection type is suitable for devices using voltage outputs, such as 0-5 V or 0-10 V.
The main advantage of the 3-wire connection is its improved stability and measurement accuracy, particularly in applications with long cable runs and varying load resistances. It requires a slightly more complex wiring configuration than the 2-wire system.
3, 4-Wire Connection:
The 4-wire system stands out among the rest when it comes to delivering the highest performance in pressure sensor electrical connections. The 4-wire connection, the four-terminal sensing, employs two pairs of wires for current supply and voltage measurement. This isolation eliminates errors caused by resistance in the wires, enhancing the measurement precision significantly.
The 4-wire configuration is primarily used in applications requiring exceptionally accurate and stable measurements, such as laboratory equipment or precision sensing devices. While offering ultimate precision, it is also the most complex and costly connection system among the three.
In conclusion, each connection type – 2-wire, 3-wire, and 4-wire – offers unique benefits and has its specific applications. The simplicity and cost-efficiency of 2-wire systems make them suitable for standard industrial applications, while the improved stability and versatility of 3-wire connections cater to applications with long cable runs and variable load resistances. For ultimate precision and performance, a 4-wire connection is the ideal choice.
Essential Electrical Components
Strain Relief Devices:
Avoiding Mechanical Stress and Damage, strain relief devices have been instrumental in preserving pressure sensor integrity. These devices minimize mechanical stress on electrical connections caused by bending, twisting, and pulling of the cables.
Strain relief devices enhance reliability and extend the sensor’s lifespan by preventing damage to the sensor’s internal wiring or solder joints. A popular strain relief design is an over-molded strain-relief, which integrates with the cable jacket and offers increased durability and protection.
Shielding Materials:
These materials prevent electromagnetic interference (EMI) from disrupting the sensor’s measurement accuracy or causing signal degradation. EMI can originate from various sources such as motors, power lines, or other electronic devices within proximity. Shielding materials, like conductive foils or braided metal sleeves, can be integrated into cable assemblies and enclosures to minimize EMI and ensure reliable data transmission in noise-sensitive applications.
Enclosures and Housings:
I’ve recognized the significance of enclosures and housings in maintaining pressure sensor performance. These components safeguard the sensor by providing environmental protection against moisture, dust, and corrosive substances.
Enclosures and housings protect mechanical connections and electrical components from physical damage due to shock, vibration, or impact forces.
Depending on the application, a variety of enclosure materials such as plastic, metal, or stainless steel, can be utilized to extend the sensor’s durability and longevity. Ensuring proper ingress protection (IP) ratings on enclosures and housings is essential for reliable performance in your application.
Common Pitfalls and Challenges
1. Identifying and Troubleshooting Connection Issues
Identifying and troubleshooting connection issues is one of the most significant challenges in pressure sensor electrical connections. These issues can arise from various factors, such as incorrect wiring, loose connections, or damaged components.
Troubleshooting these issues often involves the following steps:
- Visually inspect the connections for damage or signs of wear.
- Use a multimeter to verify the proper functioning of wires, connectors, and the pressure sensor itself.
- Check wire routing and cable management for potential noise or electrical interference sources.
- Examine the connections for any signs of corrosion or contamination and clean them if necessary.
2. Environmental Factors that Can Affect Connector Performance
Environmental factors can significantly impact the performance and longevity of pressure sensor electrical connections. These factors include temperature, humidity, vibration, and exposure to dust or chemicals. Some potential issues and how to mitigate them are:
- Temperature: Extreme temperature fluctuations may cause materials to expand or contract, resulting in loose connections. Ensure that the connectors and components are rated for the operating temperature range of the environment.
- Humidity: Moisture can infiltrate connections, leading to corrosion or short-circuiting. Use connectors with appropriate ingress protection ratings and consider using conformal coatings to safeguard against moisture ingress.
- Vibration: Mechanical vibrations can loosen connections over time or damage components. Securely fasten and support connections, and use connectors designed for high-vibration environments if necessary.
- Dust and Chemicals: Contaminants can impair conductivity or cause corrosion. Choose connectors with appropriate environmental sealing properties and maintain proper cleaning and inspection routines.
3. Preventing Mechanical Stress and Strain on Connections
Mechanical stress and strain on pressure sensor electrical connections can result in damage or failure over time. To prevent these issues, you can carefully consider the following guidelines:
- Choose connectors and components that are designed to withstand the expected mechanical load and environmental conditions in the application.
- Use strain relief techniques, such as cable glands or clamps, to prevent excessive force on connectors and terminals, ensuring that the weight and movement of the cable do not impact the connections.
- Keep wire routing neat and organized, avoiding tight bends or kinks that may cause undue stress on the connections.
- Consider using flexible conduits or cable carriers in applications with significant movement or vibration to protect the connections and cables from damage.